Oil and Gas
Corrosion Challenges in Oil and Gas Operations
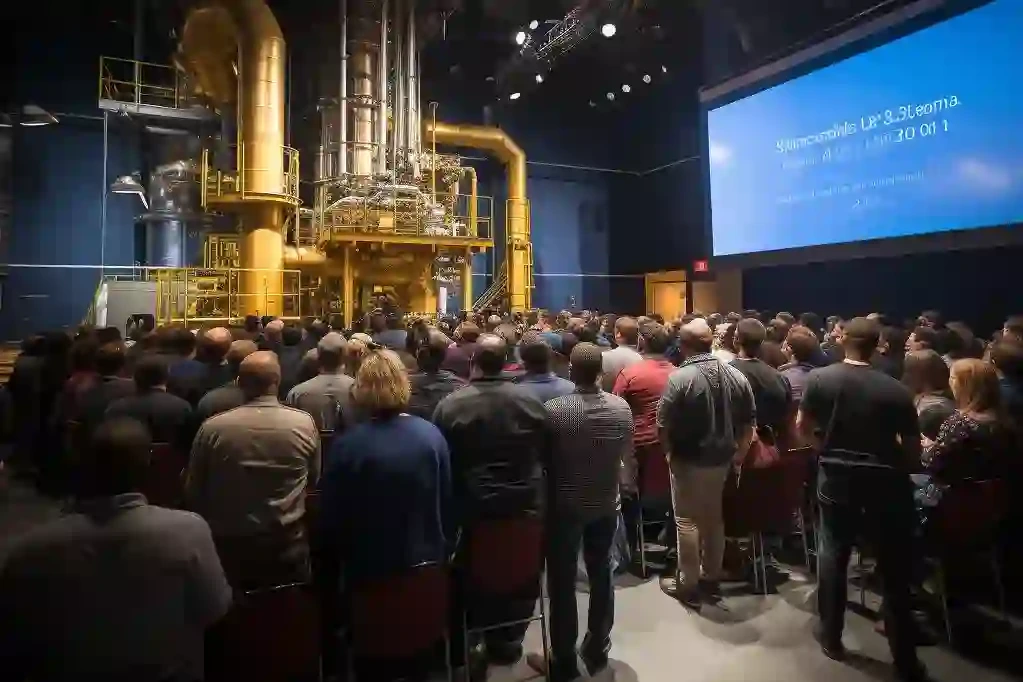
-
/home/comparecarriers/public_html/wp-content/plugins/mvp-social-buttons/mvp-social-buttons.php on line 120
- /home/comparecarriers/public_html/wp-content/plugins/mvp-social-buttons/mvp-social-buttons.php on line 123
- /home/comparecarriers/public_html/wp-content/plugins/mvp-social-buttons/mvp-social-buttons.php on line 126
- /home/comparecarriers/public_html/wp-content/plugins/mvp-social-buttons/mvp-social-buttons.php on line 129
https://compare-carriers.com/corrosion-challenges-in-oil-and-gas-operations/&t=
Warning: Undefined variable $post in /home/comparecarriers/public_html/wp-content/plugins/mvp-social-buttons/mvp-social-buttons.php on line 120
Warning: Attempt to read property "ID" on null in /home/comparecarriers/public_html/wp-content/plugins/mvp-social-buttons/mvp-social-buttons.php on line 120
Corrosion Challenges in Oil and Gas Operations', 'facebookShare', 'width=626,height=436'); return false;" title="Share on Facebook">
Corrosion Challenges in Oil and Gas Operations &url=
Warning: Undefined variable $post in /home/comparecarriers/public_html/wp-content/plugins/mvp-social-buttons/mvp-social-buttons.php on line 123
Warning: Attempt to read property "ID" on null in /home/comparecarriers/public_html/wp-content/plugins/mvp-social-buttons/mvp-social-buttons.php on line 123
https://compare-carriers.com/corrosion-challenges-in-oil-and-gas-operations/', 'twitterShare', 'width=626,height=436'); return false;" title="Tweet This Post">
https://compare-carriers.com/corrosion-challenges-in-oil-and-gas-operations/&media=
Warning: Undefined variable $post in /home/comparecarriers/public_html/wp-content/plugins/mvp-social-buttons/mvp-social-buttons.php on line 126
Warning: Attempt to read property "ID" on null in /home/comparecarriers/public_html/wp-content/plugins/mvp-social-buttons/mvp-social-buttons.php on line 126
https://compare-carriers.com/wp-content/uploads/2025/02/3928.webp&description=
Warning: Undefined variable $post in /home/comparecarriers/public_html/wp-content/plugins/mvp-social-buttons/mvp-social-buttons.php on line 126
Warning: Attempt to read property "ID" on null in /home/comparecarriers/public_html/wp-content/plugins/mvp-social-buttons/mvp-social-buttons.php on line 126
Corrosion Challenges in Oil and Gas Operations', 'pinterestShare', 'width=750,height=350'); return false;" title="Pin This Post">
Corrosion Challenges in Oil and Gas Operations&BODY=I found this article interesting and thought of sharing it with you. Check it out:
Warning: Undefined variable $post in /home/comparecarriers/public_html/wp-content/plugins/mvp-social-buttons/mvp-social-buttons.php on line 129
Warning: Attempt to read property "ID" on null in /home/comparecarriers/public_html/wp-content/plugins/mvp-social-buttons/mvp-social-buttons.php on line 129
https://compare-carriers.com/corrosion-challenges-in-oil-and-gas-operations/">
-
/home/comparecarriers/public_html/wp-content/plugins/mvp-social-buttons/mvp-social-buttons.php on line 120
- /home/comparecarriers/public_html/wp-content/plugins/mvp-social-buttons/mvp-social-buttons.php on line 123
- /home/comparecarriers/public_html/wp-content/plugins/mvp-social-buttons/mvp-social-buttons.php on line 126
- /home/comparecarriers/public_html/wp-content/plugins/mvp-social-buttons/mvp-social-buttons.php on line 129
https://compare-carriers.com/corrosion-challenges-in-oil-and-gas-operations/&t=
Warning: Undefined variable $post in /home/comparecarriers/public_html/wp-content/plugins/mvp-social-buttons/mvp-social-buttons.php on line 120
Warning: Attempt to read property "ID" on null in /home/comparecarriers/public_html/wp-content/plugins/mvp-social-buttons/mvp-social-buttons.php on line 120
Corrosion Challenges in Oil and Gas Operations', 'facebookShare', 'width=626,height=436'); return false;" title="Share on Facebook">
Corrosion Challenges in Oil and Gas Operations &url=
Warning: Undefined variable $post in /home/comparecarriers/public_html/wp-content/plugins/mvp-social-buttons/mvp-social-buttons.php on line 123
Warning: Attempt to read property "ID" on null in /home/comparecarriers/public_html/wp-content/plugins/mvp-social-buttons/mvp-social-buttons.php on line 123
https://compare-carriers.com/corrosion-challenges-in-oil-and-gas-operations/', 'twitterShare', 'width=626,height=436'); return false;" title="Tweet This Post">
https://compare-carriers.com/corrosion-challenges-in-oil-and-gas-operations/&media=
Warning: Undefined variable $post in /home/comparecarriers/public_html/wp-content/plugins/mvp-social-buttons/mvp-social-buttons.php on line 126
Warning: Attempt to read property "ID" on null in /home/comparecarriers/public_html/wp-content/plugins/mvp-social-buttons/mvp-social-buttons.php on line 126
https://compare-carriers.com/wp-content/uploads/2025/02/3928.webp&description=
Warning: Undefined variable $post in /home/comparecarriers/public_html/wp-content/plugins/mvp-social-buttons/mvp-social-buttons.php on line 126
Warning: Attempt to read property "ID" on null in /home/comparecarriers/public_html/wp-content/plugins/mvp-social-buttons/mvp-social-buttons.php on line 126
Corrosion Challenges in Oil and Gas Operations', 'pinterestShare', 'width=750,height=350'); return false;" title="Pin This Post">
Corrosion Challenges in Oil and Gas Operations&BODY=I found this article interesting and thought of sharing it with you. Check it out:
Warning: Undefined variable $post in /home/comparecarriers/public_html/wp-content/plugins/mvp-social-buttons/mvp-social-buttons.php on line 129
Warning: Attempt to read property "ID" on null in /home/comparecarriers/public_html/wp-content/plugins/mvp-social-buttons/mvp-social-buttons.php on line 129
https://compare-carriers.com/corrosion-challenges-in-oil-and-gas-operations/">
Continue Reading